Technomark, global expert in intelligent solutions for traceability and industrial marking
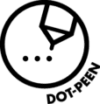

Technomark: Laser & Dot Peen Marking Solutions
Industrial Direct Part Marking Equipment for Reliable Traceability
The right industrial marking system doesn’t just mark your products — it protects your brand, ensures compliance, and streamlines production.
Technomark provides advanced laser marking and dot peen marking solutions engineered for precision, durability, and efficiency. Whether you need a standalone marking device or a fully integrated, automated marking solution, our technology ensures permanent, high-quality part identification for even the most demanding industrial environments.
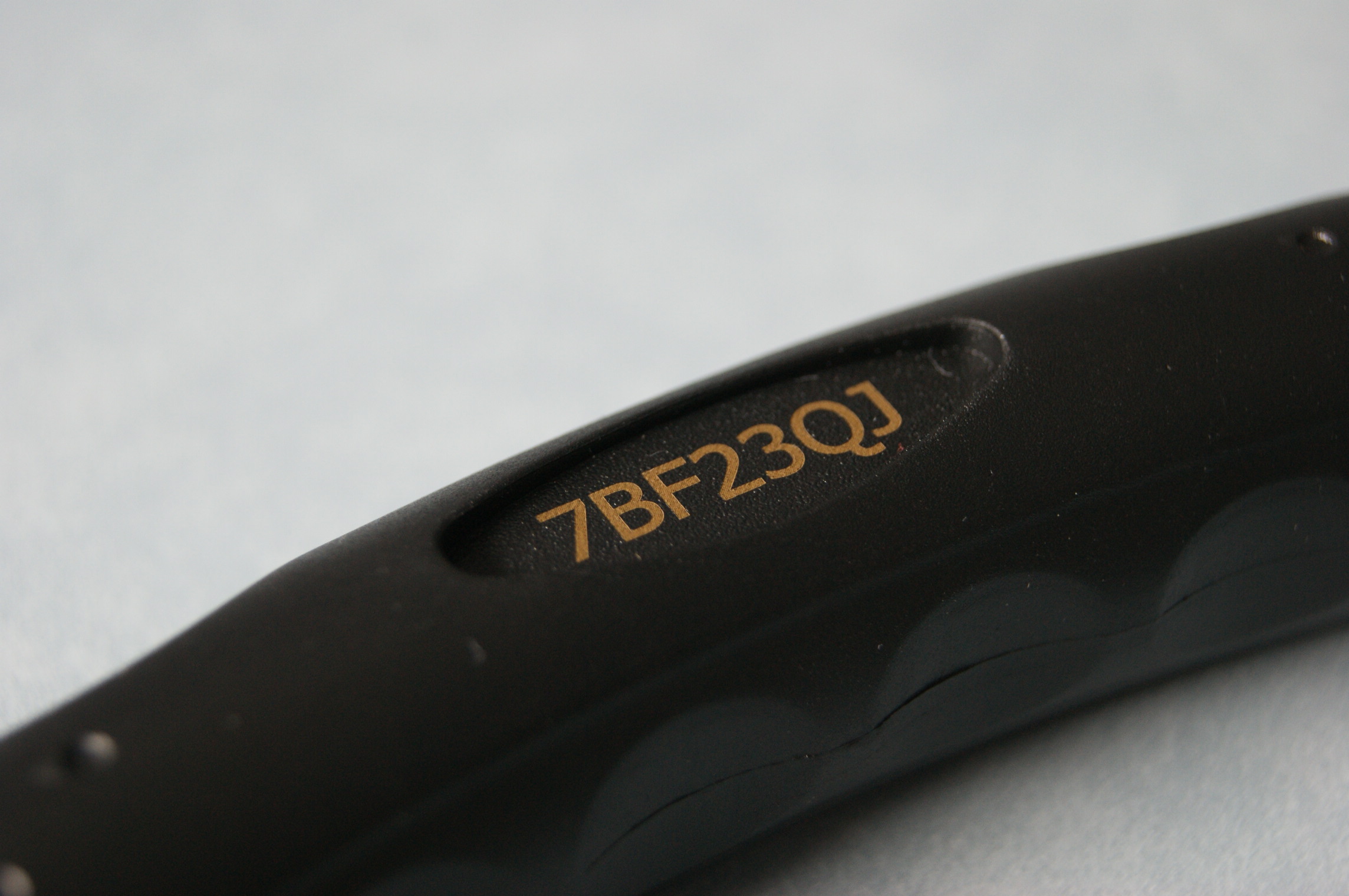
New products
Discover GX Small and XS Inline, the laser marking solutions of tomorrow
New and Ultra Compact
Laser Marking Station
New, Reduced Design
Laser Marking Equipment
Laser & Dot Peen Marking: Tailored to Your Needs
DESIGNING FOR THE APPLICATION OF TOMORROW
Laser Marking Solutions
Technomark’s industrial laser marking systems provide permanent, high-contrast marks on metal, plastic, and composites. From compact units to high-speed, automated marking solutions, we deliver the precision and efficiency modern manufacturers need.
Benefits of Laser Marking:
- Unparalleled precision and detail
- High-speed marking to increase throughput
- Non-contact process minimizes material stress
- Permanent, durable marks resistant to abrasion and chemicals
- Ideal for complex designs, barcodes, and data matrix codes
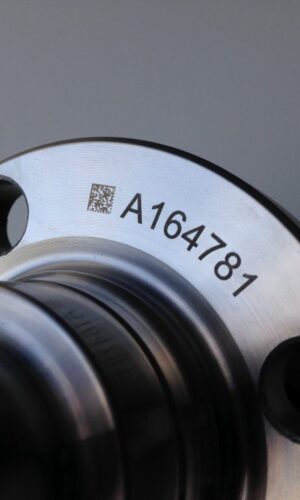
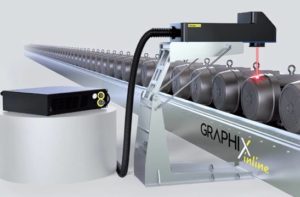
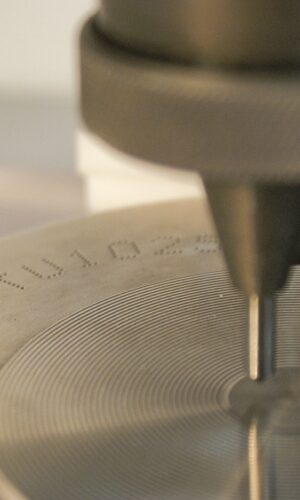
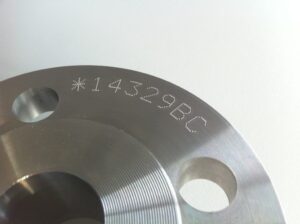
DESIGNING FOR THE APPLICATION OF TOMORROW
Dot Peen Marking Solutions
Technomark’s dot peen marking machines deliver deep, durable, and tamper-proof direct part marking. Our portable and automated solutions adapt to a variety of industrial marking needs, from serial numbers to tracking codes.
Benefits of Dot Peen Marking:
- Durable and tamper-proof marks
- Cost-effective marking solution
- Versatile marking on various materials
- Easy integration into production lines
- Ideal for deep marking and challenging surfaces
Tailored Marking Solutions for Every Industry
- Automotive
- Aerospace
- Medical Devices
- Electronics
- Oil & Gas
- Military & Defense
- Metalworking & Fabrication
WE GO FURTHER WITH YOU
Why Choose Technomark: Your Partner in Precision and Traceability
Component traceability is no longer just a good practice — it’s essential for success. That’s where we come in. Technomark is committed to helping you achieve flawless dot peen and laser marking solutions that ensure product traceability and meet industry standards.
Our systems have helped globally recognized manufacturers improve:
- Cost efficiency and reduce waste
- Quality control for top-notch products
- WIP tracking to streamline production
- Visibility across the supply chain
- Part authenticity for trusted products
- Error-proofing and assembly process improvements
- Warranty management for customer satisfaction
With over 19,000 systems in use worldwide, Technomark is your trusted partner for industrial traceability. Our permanent, clear markings ensure quality control every step of the way.
We put customers first with:
-
Feasibility studies and sample marking
-
Live demos and on-site testing
-
Custom solutions and training
-
Full support, helpline, and maintenance
-
Rental options for short-term needs
Resources
Learn More About Industrial Direct Part Marking With Our Blog
The XS Inline and GX Small: New Laser Marking Powerhouses
The XS Inline and GX Small: New Laser Marking Powerhouses Technomark is proud to offer two compact yet powerful laser marking solutions, the XS Inline and GX Small, designed to meet the evolving needs of modern production lines and standalone workstations. Whether you’re looking for seamless integration into your manufacturing line or a single-handed marking […]
More Blog ContentSelecting Materials: Laser Marking Machine Guide
Selecting Materials: Guide for Laser Marking Machines Laser marking machines are necessary in sectors where labels must withstand tough conditions and stay readable. When picking the right laser for the job, it really boils down to the materials you’re working with. Whether you’re dealing with hard metals that demand precise, enduring marks or softer materials […]
More Blog ContentIntro to Integrating Traceability Software for Manufacturing
Imagine having the ability to track every component, process, and product in your manufacturing chain with precision. TA traceability software enables manufacturers to navigate the complexities and regulatory requirements of modern production. Whether you’re a manufacturing manager, an operations director, or a quality control specialist, software traceability for manufacturing transforms how you manage your processes […]
More Blog Content