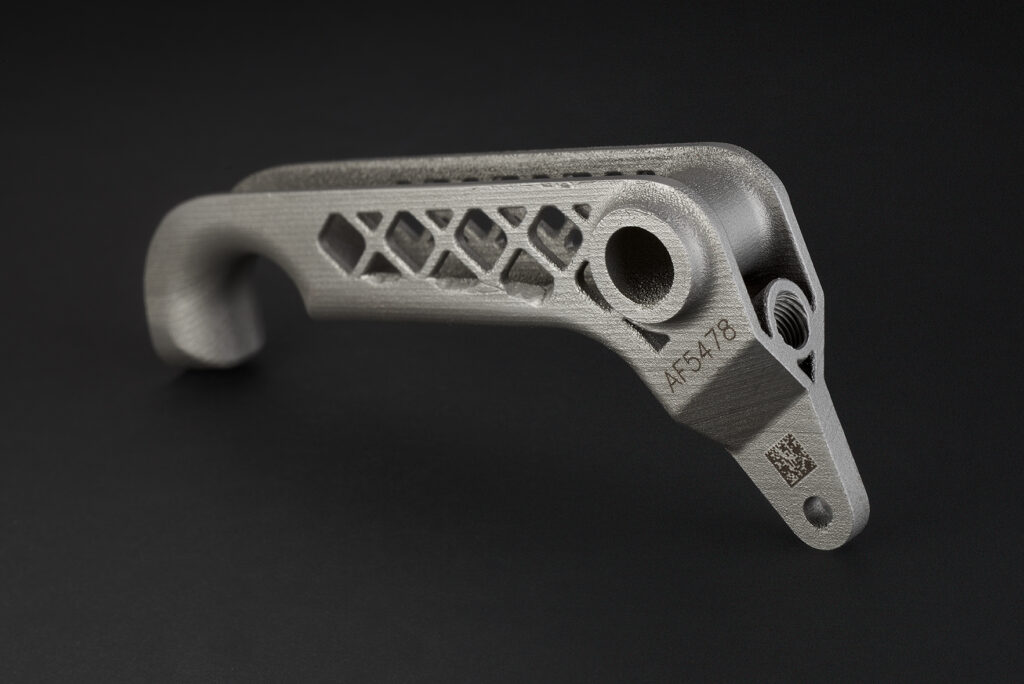
Industry codes are used for a number of processes in the manufacturing industry, but perhaps the most critical application is part marking. Part marking can be used to identify and track parts within production systems and supply chains, and there are many different types of industry codes that can be used for this purpose.
DataMatrix is one of the most popular direct part marking codes, and it’s used extensively in government and military applications due to its high-security level. The code consists of two-dimensional symbols embedded with information about the product or part being marked. This code is also resistant to environmental hazards such as UV light or chemicals, making it well-suited for harsh work environments.
Metal part marking is one of the oldest and most reliable methods for identifying components in manufacturing processes. The process involves using laser engraving technology to mark metals with various symbols or text-based codes that help identify the component being marked. Metal part marking can be done quickly and accurately, making it an ideal solution for businesses looking for an efficient way to label their parts or products.
5 Common Code Types
Metal part marking using certain code types is highly accurate, making it a reliable way to identify components for various manufacturing applications. Examples of those code types include serial numbers, which provide a way to quickly identify parts in manufacturing processes, while QR codes and DataMatrix codes offer more detailed information such as product specifications or assembly instructions.
They can also be used to track products through the supply chain or store other types of data like part or product expiration dates.
These are among the most common code types used in manufacturing:
- Serial numbers
- Barcodes
- QR codes
- UID marking
- DataMatrix codes
1. Serial Numbers
Serial numbers are a popular type of code used in metal part marking. Serial numbers provide a means of tracking individual components, allowing manufacturing companies to monitor and control production lines more effectively.
They also allow for increased traceability and accountability, as each component can be easily identified at any time during the manufacturing process. Additionally, serial numbers allow for easy inventory management, ensuring that components are properly tracked from procurement to delivery. With serial numbers, businesses can better manage their stock levels and reduce waste by proactively addressing potential issues before they become problems.
2. Barcodes
Barcodes are commonly used to provide identification for individual components manufactured by businesses. Much like serial numbers, barcodes provide a means of tracking components, allowing companies to monitor and control production lines more effectively. In addition to traceability and accountability, barcodes also provide an efficient solution for inventory management.
Businesses can easily scan barcodes to keep accurate records of their stock levels with minimal effort. Barcodes are most commonly used in the retail industry where they are scanned at the point of sale in order to easily record and manage the sale of items. They are also widely used in many other industries such as manufacturing, warehousing, and distribution operations.
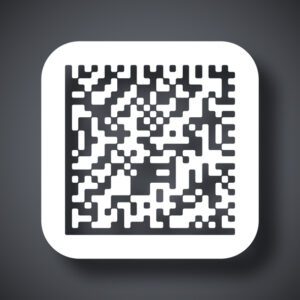
3. QR codes
QR codes are similar to barcodes but with the added benefit of storing more information. They can easily be scanned by most smartphones, making them a popular tool for marketing, product tracking, and customer engagement. QR codes are typically used for product labeling and tracking in supply chain operations. Businesses also commonly use them as a form of digital identification for their products, allowing customers to retrieve information about the item they are looking at quickly.
QR codes provide an efficient way for companies to track their products and keep accurate records while providing customers with an easy-to-use tool to access additional information about their purchases. Additionally, many consumer products are now marked with a unique QR code which allows companies to better track individual items through their entire lifecycle.
4. UID marking (Unique Identification)
UID marking, also known as Unique Identification, is an alternative to QR codes typically used in industrial and manufacturing applications. UIDs are encoded with a unique string of information that can be used to identify individual items or components within a larger production process.
This allows manufacturers to quickly and accurately track the lifecycle of their product during production, shipping, and ultimately in retail stores. In addition to providing accurate tracking of products throughout their lifespan, UID marking also offers companies the ability to access valuable data such as production date, batch code, expiration date and more. This information can then be used by companies for quality assurance purposes or for other analytics purposes.
5. DataMatrix codes
DataMatrix codes are a popular type of UID technology used in industrial and manufacturing applications. They are two-dimensional barcodes that contain encoded information regarding the product, such as production date, batch code, and expiration date.
DataMatrix codes can hold much more data than traditional linear bar codes, making it possible to identify individual items or components within a larger production process with greater accuracy. Additionally, these codes are significantly smaller than other UID types and can be read quickly, making them ideal for high-speed scanning operations.
Bring us your questions:
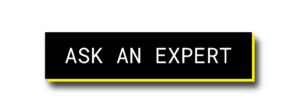
Understanding DataMatrix Code
DataMatrix codes are composed of two distinct components: the data and the error correction. The data component is a string of characters that contain information relevant to the product or item that it is associated with. This information can range from production date, to batch code and expiration date.
The error correction component, known as Error Correction Code or ECC, is used to detect any errors in the DataMatrix code, which makes it possible for scanners and other readers to still accurately read and interpret the code even if portions of it have been damaged or altered. The code is also capable of encoding a range of different data types such as numbers, text, URLs, images, and binary data.
This combination of data and error correction makes DataMatrix codes an ideal choice for UID technology in industrial and manufacturing applications. Their small size makes them easy to store while their ability to hold large amounts of data enables them to track complex production processes with greater accuracy than traditional linear bar codes. Furthermore, they can be read quickly, making them suitable for high-speed scanning operations.
DataMatrix codes are two-dimensional symbols made up of square and hexagonal modules arranged in a pattern. They can hold up to 2,335 alphanumeric characters and can be read from any direction.
DataMatrix codes are most commonly used in the automotive industry to track parts and components through the entire production process. They have also been seen in other industries such as aerospace and medical device engineering. In each of these cases, they provide detailed analytics on products throughout their lifespan and enable manufacturers to maintain accurate records of each part or component produced.
The Difference Between DataMatrix Code and QR Code
DataMatrix codes have unique shapes and sizes compared to standard barcodes and QR codes. While typical barcodes and QR codes are rectangular in shape, DataMatrix codes come in both square and circular designs. This makes them easy to distinguish from traditional barcodes and QR codes at a quick glance.
DataMatrix codes also offer better security than other types of industry coding systems due to their increased data capacity and ability to encode binary data. This makes it easier for malicious actors to decipher encoded information with the correct decryption key.
DataMatrix codes have numerous advantages over other types of coding systems. Their increased data capacity, unique shapes and sizes, and ability to encode binary data make them particularly secure against malicious actors attempting to access the encoded information. Their Error Correction Code (ECC) allows them to be scanned even if portions of the code are missing or damaged.
On the other hand, due to their increased complexity compared to standard barcodes and QR codes, DataMatrix codes require more specialized knowledge and technology for both encoding and decoding. This can lead to higher costs associated with the implementation and maintenance of the coding system.
In addition, DataMatrix codes are not as widely used as traditional barcodes and QR codes, which means that they may not be compatible with existing scanning hardware in many locations.
Best Practices for Direct Part Marking
When it comes to Direct Part Marking, proper placement and sizing of DataMatrix codes are essential for accurate scanning. In order to ensure that scanners are able to read the codes quickly and accurately, they should be placed in areas with minimal background interference.
The size of the code should be appropriate for the type of scanner being used – a code that is too small can be difficult to scan accurately. It’s important to make sure that the code is large enough so that when scanned, all of the encoded information can be captured in one pass.
It is also important to consider the durability of the code itself. DataMatrix codes are designed for applications in harsh environments, but it is still important to use a material that will resist damage from abrasion, chemicals, and extreme temperatures.
It’s also important to make sure that any direct part marking ink or other material used can withstand these conditions too. Additionally, proper application of the code is essential for readability – it must be applied correctly and completely for scanners to read it accurately.
Direct Part Marking | Navigating the Options Effectively
Direct part marking is a critical component of manufacturing processes, and it is important to understand the differences between various types of codes, including DataMatrix codes.
It’s essential to ensure the code size and material are appropriate for its intended environment, and that it is properly applied for accurate scanning. With these components in place, DataMatrix codes can provide a reliable means of identification and tracking in harsh environments.
Iron Out Your Part Marking Concerns with Technomark
Still have questions about the right code or marking approach for your product line? Consider this resource:
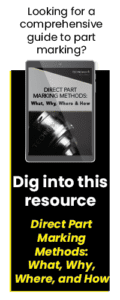